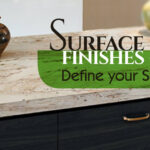
Surface Finishes that Define your Style
May 15, 2016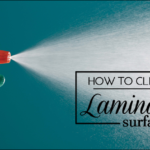
How to Clean Laminates
October 5, 2016Laminates are the go-to finishing item for modern buildingswhichprovide an ideal ambience to interiors. Laminate Sheets come at affordable prices and are easy to install.Laminates are also known as Veneer Sheets and are mostly used in furniture, counter-tops, doors, wardrobes and more.
Laminates were invented by Daniel J. O’Conor, Herbert A. Faber in 1912 and were used for insulating wires. The first flat laminate sheetswere used by the navy as casing for transmission radiosand the same was later was used asboxesof primitive TV sets. It may surprise you to know that laminates were used in aircrafts in the Second World War. Veneer sheets arenow manufactured world over and are easily the most popular fishing item for home and commercial builds.
Today, Laminates are sold under different brand names like Formica, Greenlam, Merino and Century. They are now manufactured with admirable textures, fancy designs and a varied range of colours. Understanding how Laminate sheets are made is relatively simple and the manufacturing process is quick and economical. The primary function of Laminates is to mimic the richness of rare and expensive flooring material, like wood or marble. The advantage of using veneer sheets over these traditional items is that it is economical, sustainable and environment friendly. Here are some simple processes that are employed in the manufacturing of laminates –
1. Laminate sheetslook like a layered cake in transverse section. The base layer of the cake is a hard melamine plastic that gives the VeneerSheets their stability and shape. The second layer is made of high-density fibre board (also called particle-board) which like the base layer, contains melamine that makes it moisture resistant. The third layer in Veneer Sheets is decorative and looks polished and ornamental. This is the layer that we get to see. The decorative layer has prints of high resolution wood grain, stone or tiles. This however, is not the topmost layer. The last layer, in fact, is the waterproof durable layer that protects against stains and scratches.
2. Once the layers are aligned and stacked on top of each other, they are put under immense pressure at very high temperatures. The presses have hydraulic rams that apply great pressure on the layers of raw material at temperatures reaching up to 400 degrees Fahrenheit.
3. After stacking and pressing, the laminate sheetsare now ready to cool off. After careful inspection, the laminate sheets are again stacked to cure which helps them stabilise. The planks are then profiled which involves cutting the edges for proper fitting during installation.
It is only because of the inexpensive processing that veneer sheets are now the most popular finishing item which is used across the world, in different homes, ethnicities and climatic conditions. Laminates in their most primitive and modern present form and have stood the test of time for over a century!