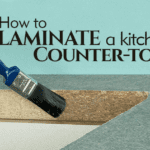
How To Laminate A Kitchen Countertop?
March 15, 2017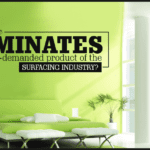
Why are laminates the most-demanded product of the surfacing industry?
April 6, 2017Remember those days when homes across households and families would look surprisingly, often mundane similar, even in a country as diverse and full of different traditional mores as ours? Well, they are long gone, especially in areas that are urban and semi urban, with higher incomes and constantly evolving design aesthetics. Some of the most important harbingers of this change are new and improved decorative laminates which have taken precedence over more expensive materials in interior design. Laminates are easy to handle, easy to install and provide a might higher number of options when it comes to textures and colours as compared to traditional materials.
For example, who would have thought, a mere decade ago that roughcast wooden and Stone textures would be popular and as easily incorporated in muted home designs as they are now? Homes have always been (more so now, than ever before) an extension of the personalities of the dwellers and homemakers. Decorative laminates are simply aiding this trend- where young, aspirational family entities are crafting the homes of their dreams with innovative textures and designs to compliment their personas.
Know Your Stuff
However, the general public is quite uninformed regarding the nature of how laminates work, what they are made of, and most importantly, how to choose a particular variety that not only complements the look and feel of the house but also adds to the utility factor of the area where it is installed. For example, laminates that are used for kitchen counter tops are supposed to be sturdy, chemically resistant to food grade acids and other substances, scratch and bacteria resistant and good to look at, all at the same time. It is vital that you be aware of these factors when you decide to go for a particular variety of laminates. Fortunately, in this age of constant connectivity, all the necessary information is always readily available online. Designer laminates are often of the post forming type. It is important that you know what that stands for.
The Gist of Laminates
Post formed laminates are slightly different in the way they are manufactured as compared to conventionally produced laminates. Post forming laminates are made to allow a certain degree of bending, so as to make way for the laminate material to become flexible. On the other hand, traditionally manufactured laminates are comparatively tougher to work with as they have a greater degree of stiffness and are much greater in girth. This makes it difficult to use in certain scenarios that require higher amounts of manoeuvrability. Post forming decorative laminates gained quite a bought of popularity in the 1950s, 1960s and were particularly famous for home decor purposes in the swinging seventies, when foreign made and designated designs started getting popular in the metropolitan cities of our country.
Now one question that must have a constant bearing on people’s minds is one concerning the exact usage of laminates especially of the post forming variety. Let us get into that in a moment.
Post forming laminates are used mostly in building cabinets and kitchen countertops. They are also used quite often on masonry slab tops and ironing boards. Post forming techniques make sure that the laminates are bent into shape easily and stay there for a prolonged period of time, ensuring durability and high degrees of reliability. However, post forming laminates are also used in places where one would never have imagined. They are used to laminate small side tables, end tables, decorative columns and even at the base of several machines used in industries. In the latter case, however, they are used purely for prevention of accidents and not to add to their visual appeal.
Let us take a look at how post formed laminates are manufactured:
Laminates, as many of our readers might already be aware, are made up of different varieties of paper. There are two kinds of paper – core paper and decorative, layered paper. Several layers of core paper and a few layers of decorative ones are pressed together into one single layer or sheet. This sheet is now brought together by soaking in adhesive resins and being subject to extremely high pressures and temperatures in specially designed presses. Then of course, when the laminates have been completely formed, they have to be softened and this is done by measured heating. This enhances the flexibility of the resin and reduces the stiffness of the material. The resins are more often than not, made up of a special substance called melamine, which respond well to heat treatment. The layers are usually soaked in phenol like substances, heated to temperatures of above 300 degrees Fahrenheit and pressurised greatly to press the layers of resin together to make one, cohesive mass. Decorative laminates of the post forming variety are quite different from stiffer varieties like traditional sunmica.
Nowadays, with an increase in the degree of automation used in the post forming process, such laminates have a higher degree of durability and reliability. Once the post forming sheets have been duly treated for higher flexibility, they are shaped and cut into various dimensions using mechanised trimmer saws. Usually, the process of cutting is done length wise to achieve grain cohesion and prevent premature disintegration of the laminate resin.
Once the laminate has been shaped and cut, it is time to make sure the substrate accepts the laminates easily. Usually, some extra formations of wood aptly named “built down sticks” are made and attached to the underside of the receiving substrate. These sticks act like guide rails and help in shaping the laminate on the counter top. Once this process is through, the countertop or cabinet panel simply has to be dropped into position, depending upon the design that has to be implemented. Usually, the binding material and the backsplash is almost always present. This is slightly better than using a traditional stiff laminate for which backsplash has to be added separately for each addition of laminate. In most cases, post formed laminates need a certain degree of end capping, essentially, making sure that there are no jagged edges that can put the user in harm’s way. However, if there is an end to display, there will be no end capping to be done. Aesthetics almost always trumps practicality in our visually dominated world!
One of the new forms of post forming laminates are flex and micro-flex post forming laminates.
So why do people have a preference for post formed laminates? Simply because aesthetics dictates that jagged edges and openly visible seams are not pleasing to the eye. On any surface, sharp edges make for an unsophisticated and uneasy look. Seamless finishes are always welcome. Long term use may make post formed laminates less flexible, but certain varieties, especially manufactured by companies that have built a reputation for themselves over the years, stay for really long periods of time without any need of refitting or renovation. Designerlaminates these days are usually always post formed, especially if they are based on wood finishes. However, if you are looking for roughcut, stone finished laminates, you might be hard pressed to find seamless finishes. Same goes for suede finishes where seams are actually beneficial to the overall look, rather than a hindrance.
One of the most important considerations in using post formed laminates is the substrate that is used. Any substrate that is to be considered should have easily workable edge machining capabilities. This is essential in producing clean edges with the smallest amount of broken edges. This is very important if one has to produce the ideal transition from flat tops to rounded edge portions. Some of the materials that can be used are: Chipwood, MDF boards, Plywood and solid nose bits. If chipwood is to be used in producing the designerlaminates, it must possess a smooth surface finish. There should be no provision of chip materials tearing out of the laminate material – the material has to have good cohesive properties and have a clean, smooth surface with no empty spaces. To maintain quality, simple brushing of the edges is often quite enough for such chipwood substrates. MDF, on the other hand, is one of the most easily machine-able materials available for laminate production. Plywood, although popular for the obvious economic advantage, is more difficult to machine into a particular shape of profile. Since there is a lot of grain work in play, plywood might also produce cutter profiles with jagged edges. To get rid of such tendencies, sanding with the best quality of sand paper available in the market, is essential. Along with this, regular cleaning and de-greasing of blades is a very important procedure. Decorativelaminateswhich need a greater radius of turn should have substrates formed of solid nose bits.
If they are used in conjunctionwith wooden floors and home decor, however, they can make for a sophisticated look and add depth to otherwise mundane interior designs. Thus, formidable decor and contemporary designs are taking the world by storm.